What is Porosity in Welding: Typical Sources and Effective Solutions
Porosity in Welding: Identifying Common Issues and Implementing Best Practices for Prevention
Porosity in welding is a prevalent issue that frequently goes unnoticed until it causes significant issues with the honesty of welds. This common flaw can endanger the stamina and longevity of welded frameworks, positioning safety and security risks and bring about expensive rework. By comprehending the origin creates of porosity and implementing reliable prevention approaches, welders can substantially improve the high quality and reliability of their welds. In this discussion, we will certainly explore the vital variables adding to porosity formation, analyze its detrimental effects on weld efficiency, and talk about the finest techniques that can be taken on to decrease porosity occurrence in welding procedures.
Typical Reasons For Porosity

Utilizing unclean or wet filler products can present pollutants right into the weld, contributing to porosity concerns. To alleviate these typical reasons of porosity, comprehensive cleaning of base metals, appropriate shielding gas selection, and adherence to ideal welding parameters are important practices in accomplishing premium, porosity-free welds.
Effect of Porosity on Weld Quality

The visibility of porosity in welding can dramatically endanger the structural integrity and mechanical buildings of bonded joints. Porosity produces voids within the weld steel, damaging its overall strength and load-bearing capacity.
One of the primary effects of porosity is a reduction in the weld's ductility and toughness. Welds with high porosity degrees have a tendency to exhibit reduced effect strength and lowered capacity to warp plastically prior to fracturing. This can be especially concerning in applications where the welded parts go through dynamic or cyclic loading problems. Porosity can impede the weld's capability to effectively transfer forces, leading to premature weld failing and potential safety and security risks in crucial frameworks. What is Porosity.
Ideal Practices for Porosity Prevention
To improve the structural integrity and quality of welded joints, what details procedures can be executed to minimize the event of porosity throughout the welding process? have a peek at this website Utilizing the appropriate welding technique for the details material being welded, such as readjusting the welding angle and weapon placement, can further avoid porosity. Normal evaluation of welds and prompt remediation of any type of issues identified during the welding procedure are crucial methods to avoid porosity and generate high-grade welds.
Importance of Correct Welding Techniques
Carrying out correct welding techniques is vital in making certain the architectural honesty and top quality of bonded joints, constructing upon the foundation of effective porosity avoidance actions. Excessive warm can lead to boosted porosity due to the entrapment of gases in the weld swimming pool. Additionally, utilizing the ideal welding parameters, such as voltage, present, and travel rate, is critical for attaining sound welds with very little porosity.
Moreover, the selection of welding procedure, whether it be MIG, TIG, or stick welding, ought to align with the details needs of the task to ensure ideal outcomes. Proper cleaning and preparation of the base metal, along with selecting the right filler material, are also vital components of proficient welding methods. By adhering to these ideal practices, welders can decrease the risk of porosity development and create you could try here top quality, structurally audio welds.
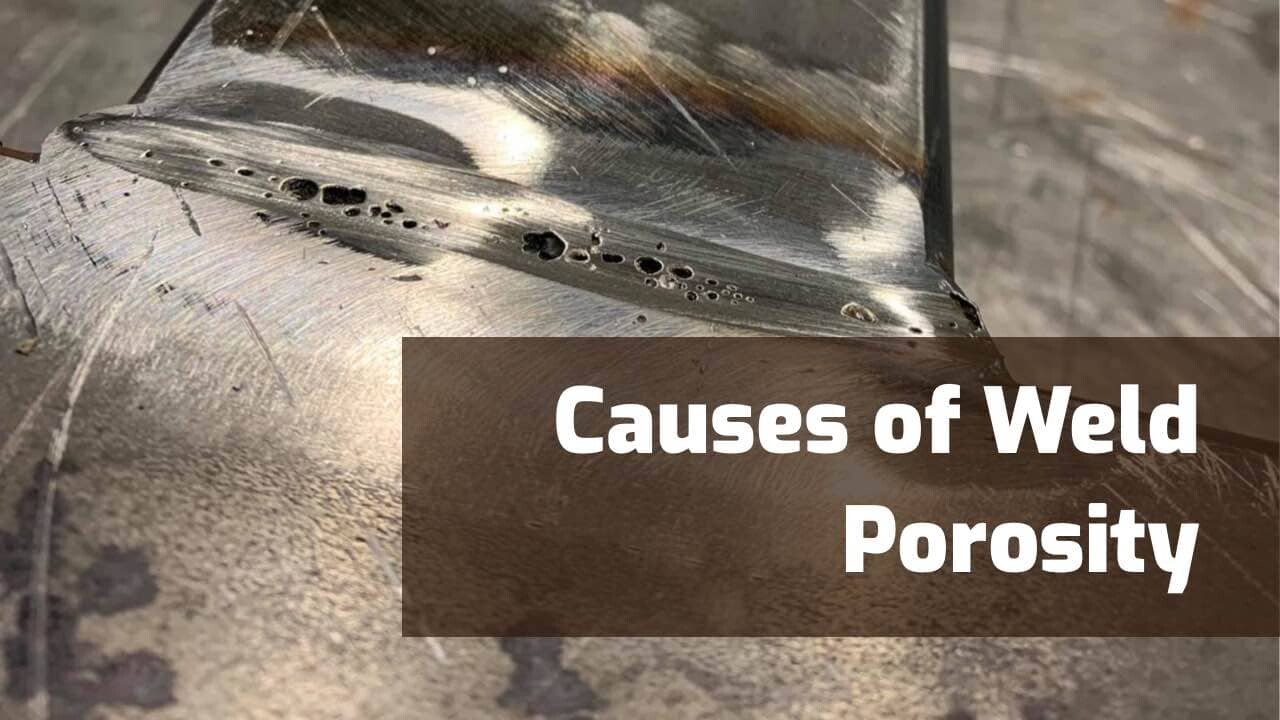
Checking and Quality Assurance Actions
Examining treatments are vital to discover and avoid porosity in welding, ensuring the stamina and toughness of the last item. Non-destructive screening approaches such as ultrasonic screening, radiographic testing, and visual examination are typically utilized to identify possible flaws like porosity.
Post-weld evaluations, on the other hand, examine the this content last weld for any flaws, consisting of porosity, and confirm that it satisfies defined criteria. Executing an extensive top quality control strategy that includes detailed screening procedures and inspections is extremely important to minimizing porosity issues and ensuring the general quality of bonded joints.
Final Thought
To conclude, porosity in welding can be a typical issue that influences the high quality of welds. By identifying the common reasons of porosity and executing ideal methods for prevention, such as appropriate welding methods and testing steps, welders can guarantee premium quality and trustworthy welds. It is necessary to focus on avoidance techniques to lessen the occurrence of porosity and keep the integrity of bonded frameworks.